V/KSM
Vacuum Relief Valve made of plastic
- 10% technology for minimum pressure increase up to full lift
- extreme tightness, resulting in lowest possible product losses and reduced environmental pollution
- set pressure close to opening pressure for optimum pressure maintenance in the system
- valve pallet is guided inside the housing to protect against harsh weather conditions
- non-corrosive
- especially suitable for aggressive, sticky, or polymerizing substances
- weight reduction in comparison to steel/stainless steel
- high surface quality
- automatic condensate drain
- different plastics can easily be combined
- maintenance-friendly design
Function and Description
The PROTEGO® valve V/KSM is a state-of-the-art vacuum relief valve with excellent flow performance made of high-grade synthetic material. It is used as a device to relieve vacuum in tanks, containers, and process engineering equipment. It prevents the in-breathing of air until reaching the set pressure. The valve is a perfect solution for corrosive, polymerizing, or sticky substances.
The device will start to open as soon as the set pressure is reached and is fully open within 10% pressure increase. Continuous investments in and a commitment to research and development have allowed PROTEGO® to develop a low pressure valve which has the same opening characteristic as a high pressure safety relief valve. This “full lift type” technology allows the valve to be set at just 10% below the maximum allowable working vacuum (MAWV) of the tank and still safely vent the required mass flow.
Due to our highly developed manufacturing technology, the tank pressure is maintained up to the set pressure with a seal that is far superior to the conventional standard. This feature is achieved by valve seats made of high-performance plastics and a high grade PTFE seal. After the vacuum is released, the valve re-seats and provides a tight seal.
The optimized fluid dynamic design of the valve body and valve pallet is a result of many years of research, resulting in a stable operation of the valve pallet, optimized performance, and reduced product losses.
Dimensions
To select the nominal size (DN), use the flow capacity chart on the following page
DN | 50 / 2" | 80 / 3" | 100 / 4" | 150 / 6" | 200 / 8" |
a | 57 / 2.24 | 77 / 3.03 | 87 / 3.43 | 126 / 4.96 | 180 / 7.09 |
a | (115 / 4.53)* | (146 / 5.75)* | (175 / 6.89)* | ||
b | 259 / 10.20 | 376 / 14.80 | 373 / 14.69 | 460 / 18.11 | 469 / 18.46 |
b | (338 / 13.31)* | (427 / 16.81)* | (437 / 17.20)* | ||
c | 150 / 5.91 | 200 / 7.87 | 225 / 8.86 | 280 / 11.02 | 350 / 13.78 |
d | 180 / 7.09 | 250 / 9.84 | 300 / 11.81 | 350 / 13.78 | 560 / 22.05 |
d | (405 / 15.94)* | (500 / 19.68)* |
Material selection for housing
Design | A | B | C |
Housing | PE | PP | PVDF |
Valve seat | PE | PP | PVDF |
Sealing | FPM | FPM | FPM |
Valve pallet | A, C, D | B, C, D | C, D |
Material selection for vacuum valve pallet
Design | A | B | C | D |
Pressure range [mbar] [inch W.C.] | +6.0 up to +16 +2.4 up to +6.4 | +5.5 up to +16 +2.2 up to +6.4 | +9.5 up to +30 +3.8 up to +12 | +30 up to +100 +12 up to +40 |
Valve pallet | PE | PP | PVDF | Hastelloy |
Sealing | PTFE | PTFE | PTFE | PTFE |
Spindle guide | PE | PP | PVDF | Hastelloy |
Weight | PE | PP | PVDF | Hastelloy |
Flange connection type
EN 1092-1; Form B1 |
ASME B16.5 CL 150 F.F. |
Design Types and Specifications
The valve pallet is weight-loaded, and the highest pressure levels are only attained with metal discs.
Vacuum valve in basic design |
Additional special devices available upon request.
Settings
Vacuum: | -6.0 mbar | -100 mbar | |
-2.4 inch W.C. | -40 inch W.C. | ||
-4.0 mbar | -100 mbar | ||
-1.6 inch W.C. | -40 inch W.C. | ||
-4.5 mbar | -100 mbar | ||
-1.8 inch W.C. | -40 inch W.C. |
Flow Capacity Chart
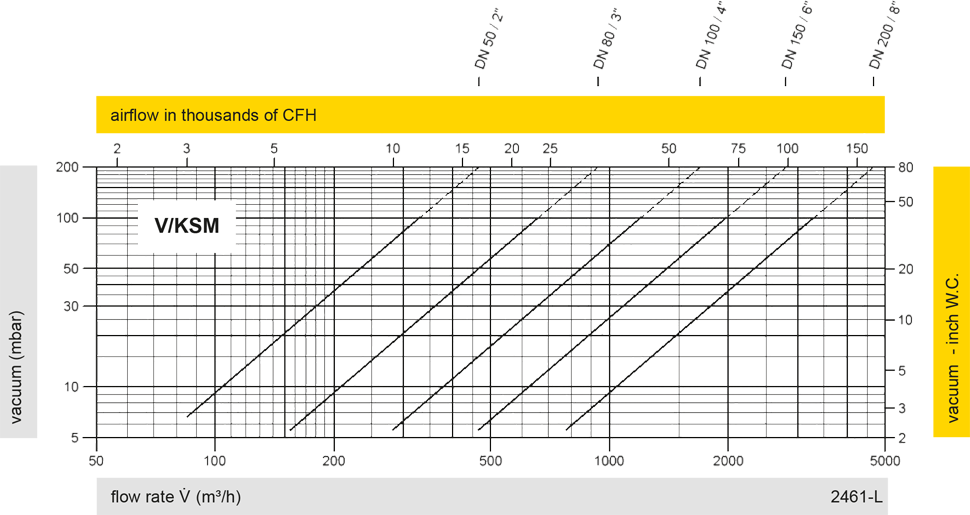
The flow capacity charts have been determined with a calibrated and TÜV certified flow capacity test rig. Volume flow V in (m³/h) and CFH refer to the standard reference conditions of air ISO 6358 (20°C, 1bar). For conversion to other densities and temperatures refer to Sec. 1: “Technical Fundamentals”.
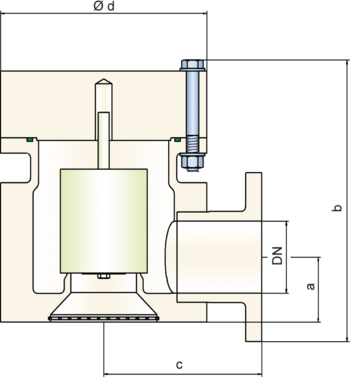