DR/SV
In-Line Detonation Flame Arrester with shut-off valve, for stable detonations and deflagrations in a straight through design, unidirectional
- protects against stabilized burning
- no expensive emergency switch-offs are required
- temperature monitoring is not necessary
- minimum number of FLAMEFILTER® discs
- easy to maintain
- the individual FLAMEFILTER® discs can be quickly removed and installed
- the FLAMEFILTER® discs can be individually replaced
- provides protection from defl agrations and stable detonations
- ideal protective system for vacuum pumps
- cost efficient spare parts
Function and Description
The PROTEGO® DR/SV flame arrester series ideally combines the function of a detonation arrester with the advantages of a shut-off valve. In case of ignition, the fire can be stabilized within the flame arrester when the flammable gas continues to flow. Inside the detonation arrester, is a valve (1) that closes in case of fire, stops the additional supply of fuel and extinguishes the flames. Temperature sensors in combination with an emergency switch off do not have to be installed if the type PROTEGO® DR/SV device is used. This device is particularly useful for the sucction-side protection of compressors and pumps.
The flame arrester protects against deflagrations and stable detonations. It can be installed anywhere in the pipe independently from the distance of the potential ignition source.
Once a detonation enters the flame arrester, energy is absorbed from the detonation shock wave by the central plate disc (2) before the flame is extinguished in the narrow gaps of the two FLAMEFILTER® discs (3). This device can be used for fluids of explosion group IIA (NEC group D).
The in-line detonation flame arresters are unidirectional and equipped with a threaded connection. The thread can be executed to international standards. The standard design can be used up to an operating temperature of +60°C / 140°F and an (absolute) operating pressure up to 1.1 bar / 15,9 psi.
EU conformity according to the currently valid ATEX directive. Approvals according to other national/international regulations on request.
Dimensions
To select the nominal size (DN), please use the flow capacity chart on the following page
DN | G ½" | G ¾" |
a | 115 / 4.53 | 115 / 4.53 |
b | 100 / 3.94 | 100 / 3.94 |
Material selection for housing
Design | A | B |
Housing | Brass | Stainless Steel |
Gasket | WS 3822 | WS 3822 |
Flame arrester unit | A | A, B |
Material combinations of flame arrester unit
Design | A | B |
FLAMEFILTER®* | Stainless Steel | Stainless Steel |
Spacer | Stainless Steel | Stainless Steel |
Support for FLAMEFILTER® | Brass | Stainless Steel |
Washer | Brass | Stainless Steel |
Selection of explosion group
MESG | Expl. Gr. (IEC / CEN) | Gas Group (NEC) |
> 0,90 mm | IIA | D |
Selection of max. operating pressure
DN | G ½" | G ¾" |
Pmax | 1,1 / 15.9 | 1,1 / 15.9 |
Specification of max. operating temperature
≤ 60°C / 140°F | Tmaximum allowable operating temperature in °C |
- | Designation |
Type of connection
Pipe thread DIN ISO 228-1 | DIN |
Flow Capacity Chart
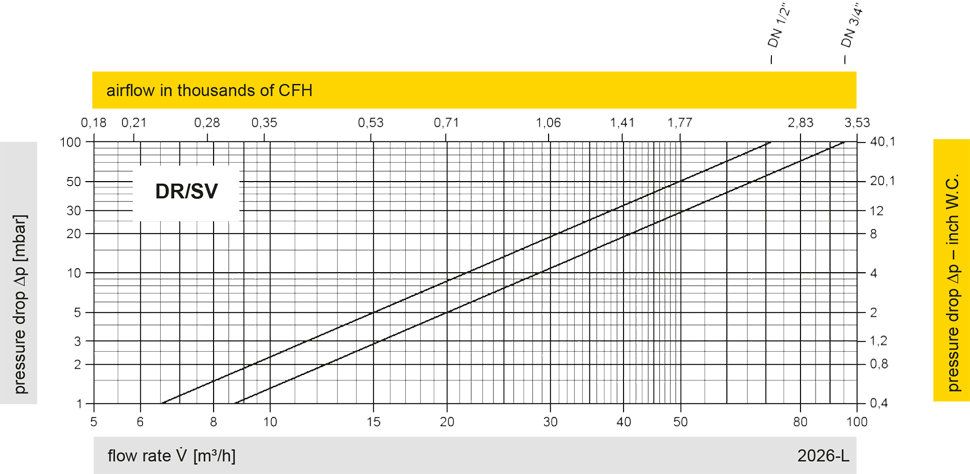
The flow capacity charts have been determined with a calibrated and TÜV certified flow capacity test rig. Volume flow V in (m³/h) and CFH refer to the standard reference conditions of air ISO 6358 (20°C, 1bar). For conversion to other densities and temperatures refer to Sec. 1: “Technical Fundamentals”.
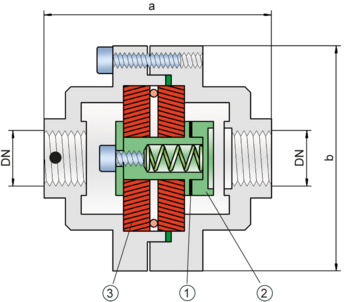
