DE/S-IIB3
High Velocity Pressure Relief Valve deflagration- and endurance burning-proof
- pressure is set with corrosion resistant permanent magnet
- jump characteristic within minimum overpressure to a full lift
- excellent tightness for minimum product loss and environmental pollution
- set pressure very near to the relieving pressure enables optimum pressure maintenance in the system
- can be used as a protective system according to ATEX in areas subject to an explosion hazard
- protection against atmospheric deflagrations and endurance burning
- high flow capacity
- maintenance-friendly design
- internal parts protected by bellows
- manual lift gear to pop valve cone
- side connection for a vacuum relief valve
- design promotes rain water drainage
- prevents gas build up on deck
- specially developed for in land water way barges
Function and Description
The deflagration- and endurance burning-proof PROTEGO® DE/S type device is a state of the art high velocity vent valve working on the principle of a dynamic flame arrester. It is primarily used as a device for flame transmission proof venting of cargo spaces and loading systems for inland waterway vessels during the loading process and on the journey. The valve offers reliable protection against excess pressure, prevents product losses almost up to the set pressure and provides protection against atmospheric deflagrations as well as endurance burning if stabilized burning occurs. The PROTEGO® DE/S high velocity vent valve is available for substances of explosion group IIB3 (NEC group C MESG ≥ 0.65 mm).
The valve cone (1) is kept in a closed position by a corrosion resistant permanent magnet (2). The set pressure is adjusted by the distance of the permanent magnet to its counterpart (3). Upon reaching the set pressure, the valve opens directly to a full lift with only a minor pressure rise (jump characteristic). The set pressure is therefore very close to the maximum allowable working pressure (MAWP) of the cargo space.
The tank pressure is maintained up to the set pressure with a tightness that is far superior to the conventional standard due to our state of the art manufacturing technology. This feature is ensured by valve seats made of high-quality stainless steel with an individually lapped valve cone. After the excess pressure is discharged, the valve reseats and provides a tight seal. The design of the valve cone and valve seat produces a vertical, free jet that transports the gases far away from the discharge opening. This keeps the deck free of gas. The shape of the valve cone and valve seat promotes the drainage of rainwater when closed. A function check of the valve is easily performed with a manual lift gear (4) which returns to its initial position after actuation. A lateral flange connection, DN2, is standard for a vacuum valve (such as the PROTEGO® SV/E-S, see volume 7).
If the set pressure is exceeded, explosive gas/product-vapour air mixtures are released to the atmosphere. When reaching the adjusted set pressure, the velocity at which the mixtures exit the valve cone gap (5) (the gap between the valve seat and the alve cone) is much higher than the fl ame velocity. If this mixture ignites, flashback into the tank is prevented. If the mixture flow continues, the dynamic flame arresting feature prevents flashback ignition even in the case of endurance burning. As the system pressure decreases, the discharge velocity at the valve cone gap decreases also. The design ensures, that even in the closing pressure range, the valve cone closes in a timely manner keeping the discharge velocity far above the fl ame velocity and thereby preventing flashback.
The valve can be used up to an operating temperature of +60°C / 140°F and meets the requirements of ADN (European Agreement concerning the International Carriage of Dangerous Goods by Inland Waterways ) for type C ships and type N ships.
EU conformity according to the currently valid ATEX directive. Approvals according to other national/international regulations on request.
Dimensions
To select the nominal size (DN), please use the flow capacity chart on the following page
DE / S with closed lateral connection DN 2 | ||||
DN 1 | 80 / 3" | 100 / 4" | 150 / 6" | |
a | 515 / 20.28 | 515 / 20.28 | 515 / 20.28 | |
b | 195 / 7.68 | 195 / 7.68 | 195 / 7.68 | |
c | 220 / 8.66 | 220 / 8.66 | 220 / 8.66 | |
d | 120 / 4.72 | 120 / 4.72 | 120 / 4.72 | |
e1 | 145 / 5.71 | 145 / 5.71 | 145 / 5.71 | |
DE / S with lateral connection for vacuum relief valve DN 2 | ||||
DN 1 | 80 / 3" | 100 / 4" | 150 / 6" | 150 / 6" |
DN 2 | 80 / 3" | 80 / 3" | 80 / 3" | 150 / 6" |
a | 515 / 20.28 | 515 / 20.28 | 515 / 20.28 | 515 / 20.28 |
b | 195 / 7.68 | 195 / 7.68 | 195 / 7.68 | 195 / 7.68 |
c | 220 / 8.66 | 220 / 8.66 | 220 / 8.66 | 220 / 8.66 |
d | 120 / 4.72 | 120 / 4.72 | 120 / 4.72 | 120 / 4.72 |
e2 | 100 / 3.94 | 100 / 3.94 | 100 / 3.94 | 100 / 3.94 |
Material selection
Design | A | B | D |
Housing | Steel | Stainless Steel | Hastelloy |
Valve seat | Stainless Steel | Stainless Steel | Hastelloy |
Valve cone | Stainless Steel | Stainless Steel | Hastelloy |
Bellow | PTFE | PTFE | PTFE |
Gasket | PTFE | PTFE | PTFE |
Selection of explosion group
MESG | Expl. Gr. (IEC / CEN) | Gas Group (NEC) |
≥ 0,65 mm | IIB3 | C |
Flange connection type
EN 1092-1; Form B1 |
ASME B16.5 CL 150 R.F. |
Design Types and Specifications
There are two different designs:
Pressure relief valve, basic design | DE/S - |
Pressure relief valve with lateral connection for vacuum relief valve | DE/S -...- * |
* additional DN 2 information
Additional special designs upon request
Settings
10 kPa | 50 kPa | ||
+40 inch W.C. | +200 inch W.C. |
Flow Capacity Chart
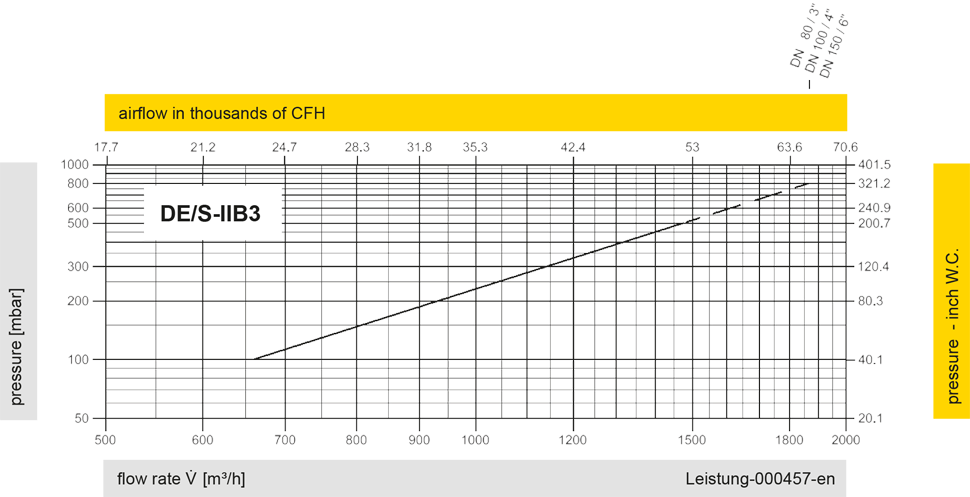
The flow capacity charts have been determined with a calibrated and TÜV certified flow capacity test rig. Volume flow V in (m³/h) and CFH refer to the standard reference conditions of air ISO 6358 (20°C, 1bar). For conversion to other densities and temperatures refer to Sec. 1: “Technical Fundamentals”.
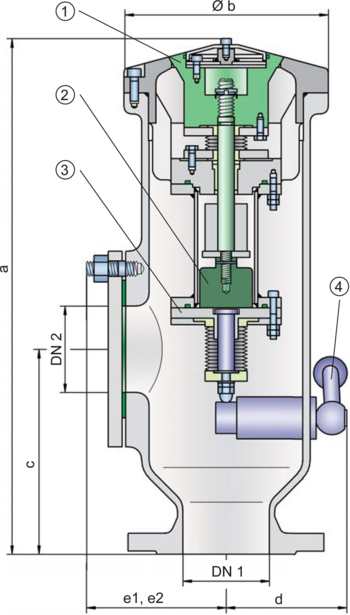
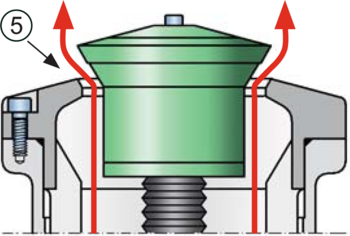