UB/SF-IIA1
Pressure/Vacuum Diaphragm Valve with internal coating, deflagration- and endurance burning-proof
- high performance seal reducing product loss below EPA’s 500ppm rule preventing environmental pollution
- set pressure close to opening pressure enables optimum pressure maintenance in the system
- can be used as a protective system according to ATEX directive in areas subject to an explosion hazard
- protection against atmospheric deflagrations and endurance burning for products up to explosion group IIA1
- flame-transmission-proof venting of the pressure chamber
- freeze protection at sub-zero conditions
- self draining function for condensate
- liquid column height is monitored by level indicators
- easy maintenance through hinged vent cap
- the modular design enables individual diaphragm to be replaced
- can be applied in biogas plants due to internal coating
- permanent refilling of the frost-proof liquid is not necessary, liquid remains within the valve chambers
- spray nozzle for internal cleanig and avoidance of foam upon request
Función y Descripción
The deflagration- and endurance burning-proof PROTEGO® UB/SF-IIA1 type diaphragm valve is a state of the art pressure and vacuum- relief valve combining the function of a dynamic flame arrester. Worldwide this design is unique. It is primarily used within biogas plants as a device for flame transmission proof in- and outbreathing on tanks, containers and process engineering apparatus. The valve offers reliable protection against excess pressure and vacuum, prevents the inbreathing of air and product losses almost up to the set pressure and protects against atmospheric deflagration and endurance burning if stabilized burning occurs. The set pressure is adjusted with a freeze resistant water glycol mixture, which assures safe operation under extreme cold weather conditions. The liquid is capsuled and is not discharged or diluted during operation. The valve can also be operated at temperatures lower than 0°C without ice constricting the funktion of the valve.
When the pressure in the tank reaches the set pressure, the FPM-diaphragm (1) on the outer valve seat ring (2) is lifted and vapours vent to the environment. The set pressure is adjusted by the liquid (glycol water mixture) column height, which is filled into the outer ring chamber (3). The overpressure chamber is equipped with an opening (4) to keep the pressure in balance with the ambient pressure. If a vacuum builds up in the tank, it is transmitted through pressure balancing tubes into the vacuum chamber (5) (inner chamber). If the set vacuum, which depends on the liquid column height in the vacuum chamber, is reached the atmospheric pressure lifts the diaphragm up off the inner valve seat ring (6). Ambient air can now flow into the tank. The liquid column heights, which affect the set pressures and vacuum, can be checked by fl oating level indicators (7).
The tank pressure is maintained up to the set pressure with a tightness that is far superior to the conventional standard due to our highly developed manufacturing technology. This is achieved because the liquid loaded diaphragm presses tightly around the special designed valve seat surface area, even when the operating pressure increases. This is extremely important to reduce leakage to an absolute minimum. After the excess pressure or vacuum is discharged, the valve reseats and provides a tight seal.
If the tank pressure exceeds the adjusted set pressure, as the case may be explosive gas/product-vapour air mixtures exit. The speed at which these mixtures exit the annular gap between the diaphragm and the outer valve seat ring while overcoming the set pressure is much faster than the flame speed. If this mixture ignites, flashback into the tank is prevented. If the mixture flow continues, the dynamic flame arresting feature prevents flashback ignition even in the case of endurance burning. Even at relatively low flow rates, which occur during thermal outbreathing, the gap formed by the volumetric flow is so narrow that flames are extinguished in the gap and flashback is prevented.
The PROTEGO® UB/SF-IIA1 valve is available for substances of explosion group IIA1 - methane. The valve can be used up to an operating temperature of +60°C / 140°F and an operating pressure up to ≥3.5 mbar / 1.4 inch W.C. and meets the requirements of European tank design standard EN 14015 – Appendix L and API 2000
EU conformity according to the currently valid ATEX directive. Approvals according to other national/international regulations on request.
Dimensiones
To select the nominal size (DN), please use the flow capacity charts on the following pages
DN | pressure | pressure | 80 / 3" | pressure | pressure | 100 / 4" | pressure | pressure | 150 / 6" |
a | up to +28 mbar | up to +11.2 inch W.C. | 615 / 24.21 | up to +28 mbar | up to +11.2 inch W.C. | 645 / 25.39 | up to +25 mbar | up to +10 inch W.C. | 680 / 26.77 |
a | > +28 mbar | > +11.2 inch W.C. | 765 / 30.12 | > +28 mbar | > +11.2 inch W.C. | 795 / 31.30 | > +25 mbar | > +10 inch W.C. | 830 / 32.68 |
b | 410 / 16.14 | 485 / 19.09 | 590 / 23.23 |
Dimensions for pressure/vacuum diaphragm valves with heating coil upon request
Material for housing
Design | B |
Housing | Steel |
Coating of housing | 2 components polymere coating |
Valve top | Stainless Steel |
Heating coil (UB / SF-H-...-I) | Stainless Steel |
Valve seats | Stainless Steel |
Gasket | FPM |
Diaphragm | FPM |
Selección del grupo de explosión
MESG | Expl. Gr. (IEC / CEN) |
≥ 1,14 mm | IIA1 |
Tipo de bridas de conexión
EN 1092-1; Form B1 |
ASME B16.5 CL 150 R.F. |
Modelo y especificación
Almost any combination of vacuum and pressure settings can be utilized for the valve. The diaphragm is pressurized by liquid.
Higher pressures can be achieved upon request with a special liquid reservoir.
Pressure/vacuum diaphragm valve, basic design | UB/SF - – |
Pressure/vacuum diaphragm valve with heating coil (max. heating fluid temperature +85°C / 185°F) | UB/SF - H |
Settings:
DN 80 | +3.5 mbar | +50 mbar | |
+1.4 inch W.C. | +20 inch W.C. | ||
DN 100 | +3.5 mbar | +45 mbar | |
+1.4 inch W.C. | +18 inch W.C. | ||
DN 150 | +3.5 mbar | +46 mbar | |
+1.4 inch W.C. | +18.4 inch W.C. | ||
Vacuum | -3.5 mbar | -35 mbar | |
-1.4 inch W.C. | -14 inch W.C. |
Diagrama de flujo volumétrico
UB/SF DN80
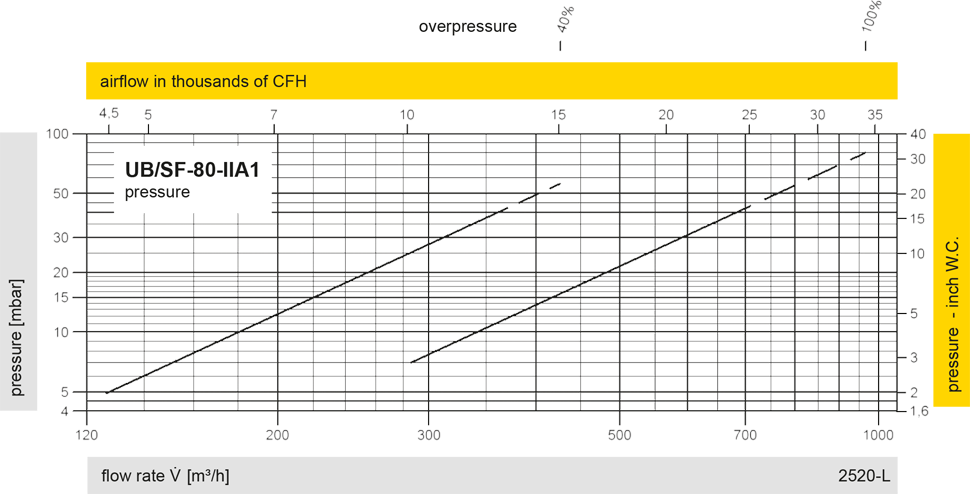
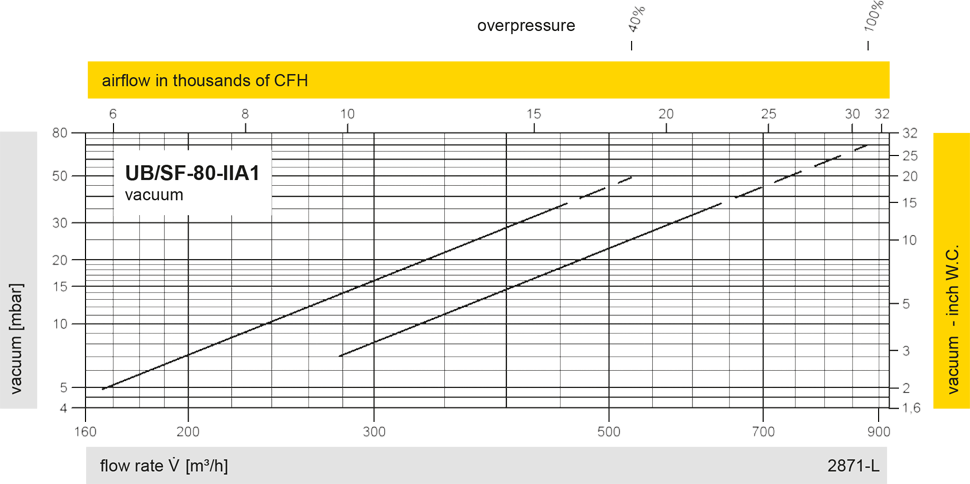
UB/SF DN100
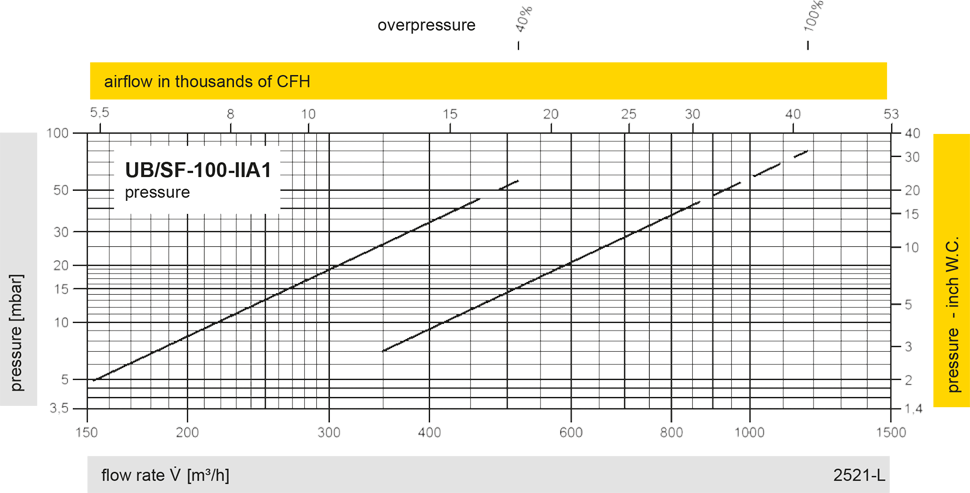
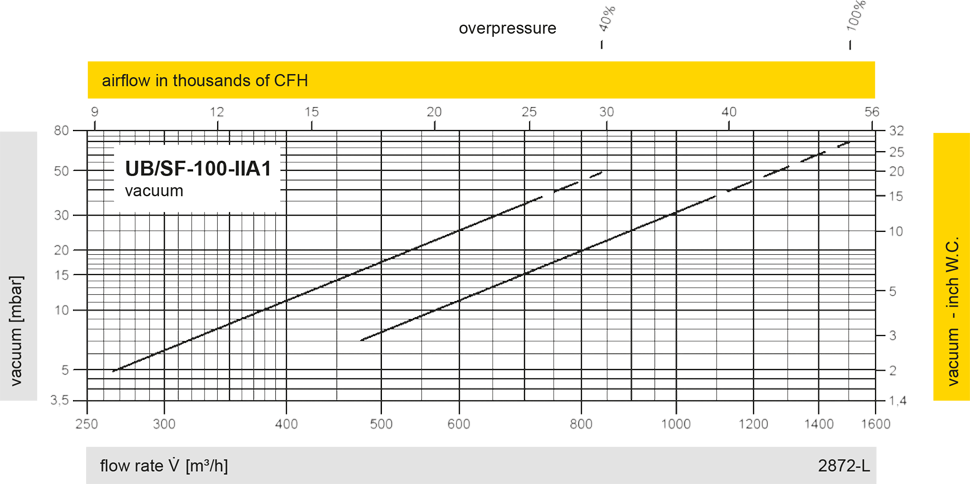
UB/SF DN150
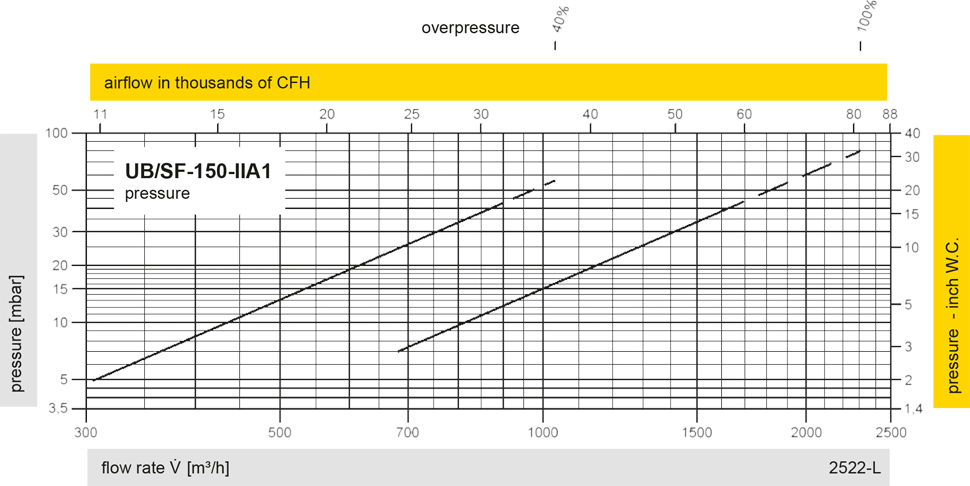
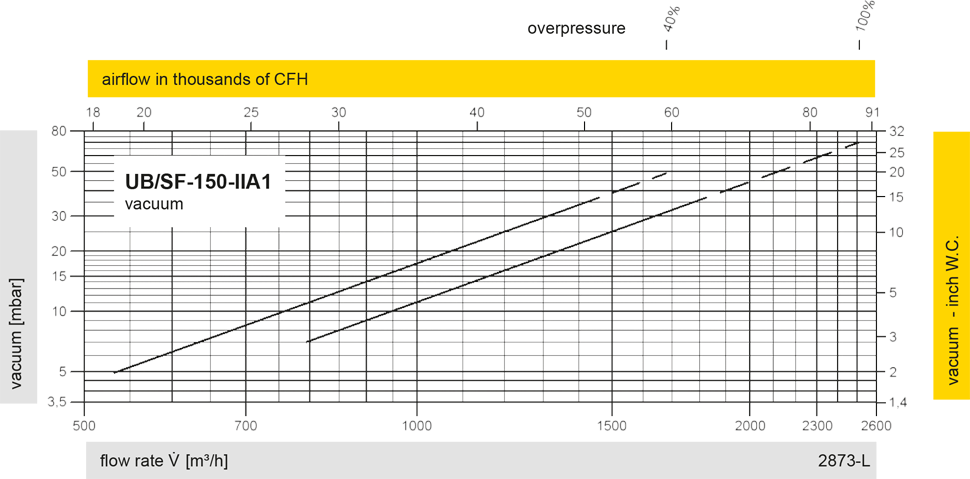

Los diagramas de flujo volumétrico han sido determinados con un banco de pruebas de caudal calibrado y certifi - cado por TÜV. El flujo volumétrico V. en [m³/h] y el CFH se refi eren a las condiciones estándar de referencia de aire según ISO 6358 (20°C, 1bar). La conversión a otras densidades y temperaturas están referidas en el Vol. 1: “Fundamentos Técnicos”.
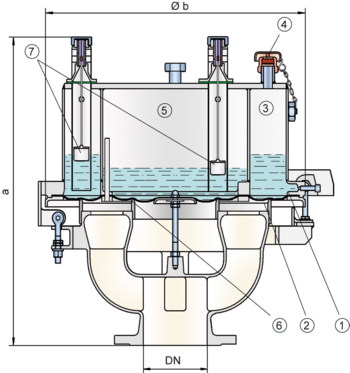